“Commitment” that transcends time and space
In the past, we have been a wooden sculpture,
shrine carpenter. We are 8th generations in the construction business,(Naka-gun, Kanagawa Prefecture). The traditional techniques of the Koshimizu family have been passed down through generations, and have been passed down to modern generations.
Furthermore, Gendai only remembers being led by the hand for walks by his grandfather, Hanzo Koshimizu, when he was 3 years old, and he was hardly given any guidance on joinery techniques. However, the second-generation Haruo Koshimizu and his great-uncle, Hidenosuke Koshimizu, were always told to move your hands'' and
move your body”, and as soon as they did something, the senior craftsmen around them told them, “this is no good”. This is not the way to do it!” When he was young, he simply made the fittings in front of him without understanding why. And what I have consistently learned is the commitment to “don’t spare any effort.”
Today, there are many factory products and ready-made fittings, but modern representatives lament that they lack the attention to detail of the past. While there are many products that focus only on productivity and are not particular about their products, our dedication to focusing on the “customer’s perspective” has supported Koshimizu’s fittings for generations. Why has such a commitment been developed? I would like to unravel its roots.
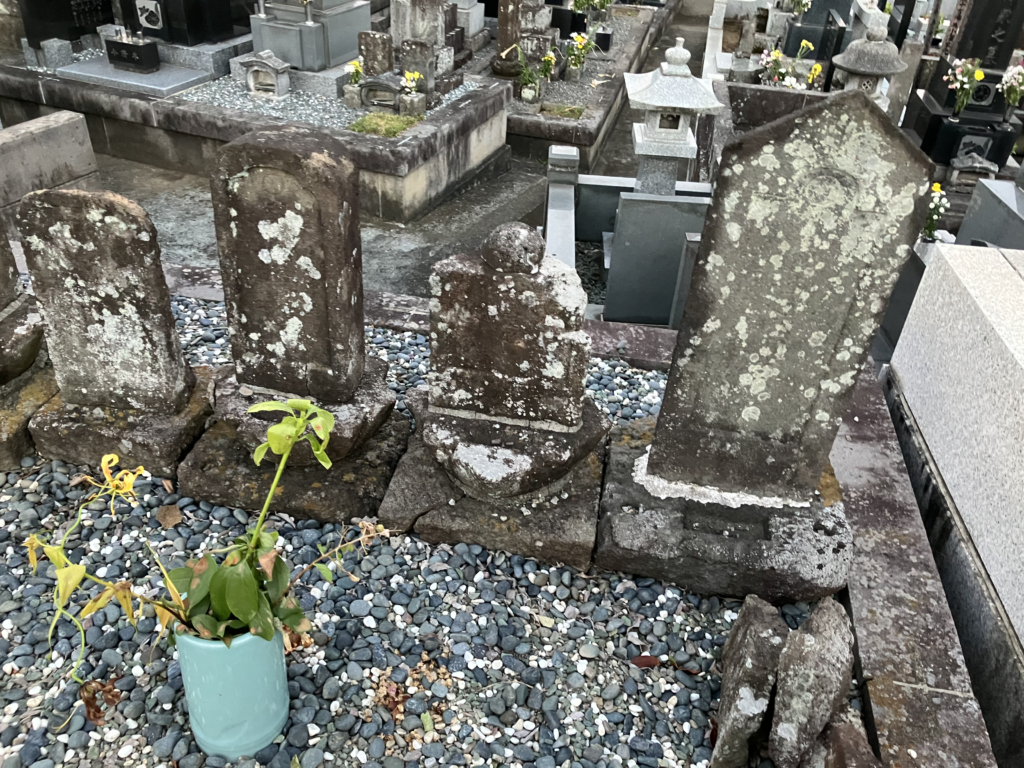
koshimizu ancestral graves
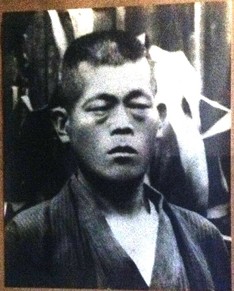
6th Hanzo Koshimizu
He was born into a family where both his father and grandfather were joiners in Nakai-cho, Naka-gun, Kanagawa Prefecture. When he was young, he traveled all over Japan to train as a warrior, and in exchange for lodging in other people’s homes during his travels, he would make and repair fittings as a thank you for the accommodation and food he received. At that time, this was called “Saigyo” and it is said by the second generation that he practiced a training method similar to that of Kobo Daishi.
After a long period of training, we moved from Nakai-cho to our current location (Ninomiya-cho, Naka-gun, Kanagawa Prefecture) and finally established a new company. At the end of the Taisho era, the first generation Koshimizu Hanzo'' was hailed as
the best in Kanto” and was affectionately known as “Ken-Han.” My experience as a Saigyo requires close communication with customers at all times.
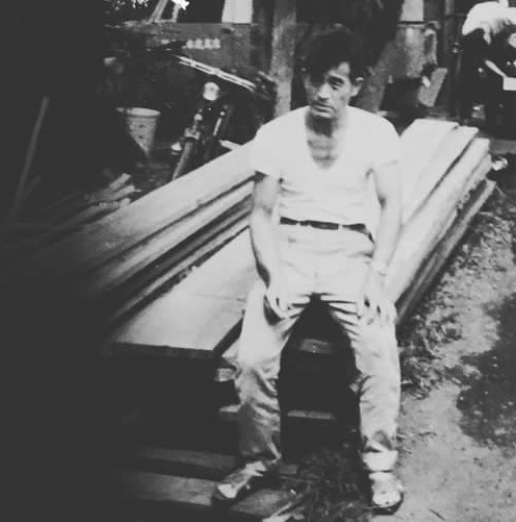
7th Haruo Koshimizu
A genius joiner who astounded the first representative, who was hailed as the best in the Kanto region, with his innovative creativity. The second generation representative, Haruo Koshimizu, was a craftsman and dedicated to his work, making the best fittings and living up to the trust of his customers. His work style is nothing short of genius, and I have seen him “drill a mortise faster than a machine” many times up close with modern tables.
Additionally, the three-kumite-style partition transom created by the second generation is a top-quality item that the first generation recognizes as surpassing his own. Furthermore, the Kozu Kumiko Buddhist altar, co-created with the younger brother of the second generation, Hidenosuke Koshimizu, is of the highest quality and is difficult to perfectly reproduce even in modern times. And it is the “invisible” commitment that modern tableware continues to amaze us with. Many joinery products use “tenons” for joining, but although the tenons are important for durability, they cannot be seen after completion. That’s why, considering profits and comfort, there was no problem at all under the laws and regulations at the time. Despite this, “two tenons” and “hell tenons,” which can never be pulled out again, are often used. This is surprising considering that there were no construction machines at the time, and the amount of work involved was enormous.
8th Shigeru Koshimizu
Born as the eldest son of the current representative, he is the current representative who carries on his father’s legacy.
His customer-oriented approach'', which has been passed down through generations of his ancestors, has earned him the deep trust of many customers, just like his predecessors, and he not only manufactures fittings, but also passionately and proactively works towards the local community that has been indebted to him for generations. I also do volunteer work. Due to his personality, one customer even says,
I want to adopt him.” Of course, he has many accomplishments and awards, and is still actively manufacturing joinery. In recent years, in order to surpass his predecessors, he has been actively selling lampshades using the Kumiko technique, which combine traditional and modern elements, and miniature fittings, which have a higher level of artistry.